Disposition de l'entrepôt pour optimiser l'impact de la chaîne d'approvisionnement
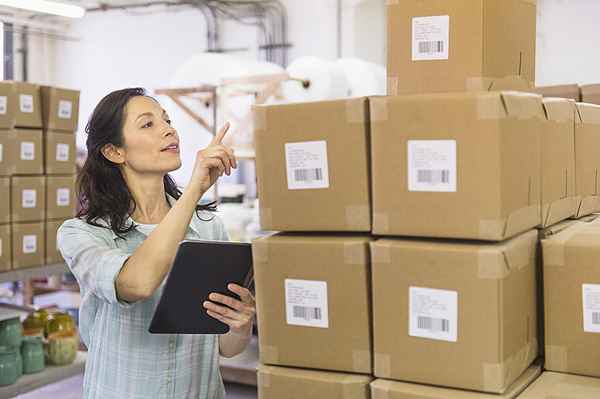
- 5093
- 1456
- Julie Prevost
La disposition d'un entrepôt peut être modifiée pour améliorer la gestion de la chaîne d'approvisionnement et les opérations d'entrepôt. Lorsqu'une nouvelle disposition d'entrepôt est proposée, un processus de planification détaillé doit être suivi pour assurer le succès du projet. Ce processus de planification devrait inclure les six étapes suivantes:
- Définir les objectifs
- Collecter des informations
- Analyser les changements nécessaires
- Créer un plan
- Mettre en œuvre le plan
- Post implémentation
Définir les objectifs de disposition de l'entrepôt
Lorsque vous décidez de la disposition d'un entrepôt, les objectifs doivent être clairement définis. Les objectifs devraient être alignés sur la stratégie globale de l'entreposage de l'entreprise. Les objectifs peuvent être définis à un niveau élevé tel que la réduction des coûts d'entreposage ou la fourniture d'un service client maximal.
De même, les objectifs peuvent être plus spécifiques, comme maximiser l'espace d'entreposage, offrir une flexibilité maximale dans l'entrepôt ou augmenter l'efficacité de l'entreposage sans augmenter les ressources.
Collecter des informations
Les informations spécifiques sur l'entrepôt proposé doivent être collectées. Cela comprend les spécifications de l'entrepôt des dessins architecturaux qui peuvent affecter le stockage et la manutention des matériaux.
Les détails doivent inclure une carte physique de l'espace d'entrepôt pour afficher des colonnes, des portes, des restrictions de hauteur, des quais et des racks de stockage. Des fonctionnalités externes qui peuvent affecter la réception, le stockage et l'expédition des matériaux doivent également être notés.
Analyser les changements nécessaires
Une fois les informations spécifiques sur l'entrepôt collectées, l'analyse peut commencer par les objectifs qui ont été définis pour la disposition de l'entrepôt. L'analyse doit déterminer si les objectifs globaux peuvent être atteints et, sinon, comment les objectifs peuvent être modifiés.
À ce stade du processus de planification, les décisions doivent être prises par la gestion des entrepôts pour déterminer quelles actions doivent être prises si les objectifs globaux ne peuvent pas être atteints ou nécessiteront des changements substantiels. Si les objectifs peuvent être atteints sur la base de l'analyse des informations, le plan de mise en œuvre détaillé peut être créé.
Créer un plan
Le plan de mise en œuvre détaillé doit afficher toutes les étapes nécessaires pour créer la disposition de l'entrepôt. Les objectifs et l'analyse des informations recueillies doivent être utilisées pour créer le plan. Le plan doit d'abord être à un niveau élevé, montrant les tâches majeures, puis chacune de celles-ci doit être subdivisée dans les tâches individuelles nécessaires.
Chaque tâche doit être examinée et allouée aux ressources appropriées, y compris l'attribution du temps estimé nécessaire pour effectuer la tâche. Le plan doit indiquer quand une tâche est tenue de démarrer et de terminer en fonction de la disponibilité des ressources - interne ou des entrepreneurs extérieurs - ou s'il dépend d'une autre tâche.
Le plan doit être vérifié pour s'assurer que toutes les dépendances ont été correctement liées. Une fois le plan créé, il doit être vérifié pour voir si le calendrier est réalisable et s'il y a suffisamment de ressources sont disponibles.
Mise en œuvre
Parfois, la disposition de l'entrepôt qui est mise en œuvre n'est pas celle qui est dans le plan. Cela peut se produire en raison de délais irréalistes dans le plan, du manque de ressources, de l'indisponibilité des entrepreneurs externes ou d'une mauvaise analyse des informations recueillies.
Pour s'assurer que le plan de disposition de l'entrepôt est obtenu, la mise en œuvre doit être chronométrée afin qu'il y ait peu ou pas de mouvement de matériaux dans l'entrepôt. Un moment idéal pour cela serait lors de l'arrêt de l'usine ou un week-end si la mise en œuvre est sur une petite taille.
Cependant, dans les entrepôts modernes, cela n'est pas toujours possible, donc souvent des ressources d'entrepôt supplémentaires sont nécessaires pour poursuivre l'expédition des produits pendant la mise en œuvre. Si tel est le cas, cela devra être pris en compte dans le plan.
La mise en œuvre doit également garantir que toutes les modifications apportées dans l'entrepôt sont reproduites dans le système de gestion des entrepôts afin que chaque article puisse être trouvé. Un inventaire physique des produits dans l'entrepôt après la mise en œuvre doit être effectué pour s'assurer que le système reflète avec précision l'entrepôt.
Post implémentation
Une fois la mise en page mise en œuvre, il devrait y avoir une série de contrôles pour s'assurer que la disposition est exactement telle que définie par les dessins approuvés. Chaque article doit être stocké en fonction du plan global et cela doit être vérifié pour s'assurer que la disposition est correcte. S'il y a des erreurs, cela pourrait entraîner des erreurs de sélection ou du matériel perdu dans l'entrepôt. L'expédition pourrait également être perturbée si les systèmes d'entrepôt n'ont pas été mis à jour avec précision avec les informations de mise en page correctes ou si les articles ont été stockés dans les mauvais endroits.
Pendant un certain temps, une fois la nouvelle mise en page mise en œuvre, des contrôles réguliers doivent être effectués pour s'assurer que la mise en page fonctionne et qu'il n'y a aucun problème opérationnel qui s'est produit en raison de la nouvelle disposition. Ces chèques devraient inclure le nombre de cycle et les stocks physiques réguliers.
- « Que fait un clerc?
- Les avantages et les inconvénients de prendre des réservations de restaurants »