Gestion totale de la qualité (TQM) et amélioration de la qualité
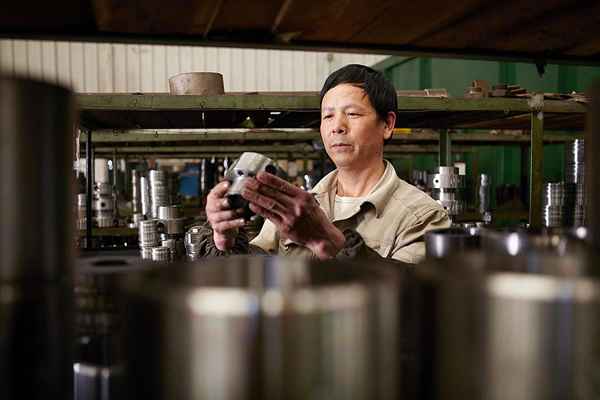
- 2196
- 185
- Mme Eva Vasseur
La gestion totale de la qualité (TQM) est une approche qui vise à améliorer la qualité et les performances qui répondront ou dépasseront les attentes des clients.
Cela peut être réalisé en intégrant toutes les fonctions et processus liés à la qualité dans toute l'entreprise. TQM examine les mesures de qualité globales utilisées par une entreprise, notamment la gestion de la conception et du développement de la qualité, le contrôle et la maintenance de la qualité, l'amélioration de la qualité et l'assurance qualité.
TQM prend en compte toutes les mesures de qualité prises à tous les niveaux et impliquant tous les employés de l'entreprise.
Origines de TQM
La gestion totale de la qualité a évolué à partir des méthodes d'assurance qualité qui ont été développées pour la première fois à l'époque de la Première Guerre mondiale. L'effort de guerre a conduit à des efforts de fabrication à grande échelle qui produisaient souvent des produits de mauvaise qualité. Pour aider à corriger cela, des inspecteurs de qualité ont été introduits sur la chaîne de production pour s'assurer que le niveau d'échecs en raison de la qualité a été minimisé.
Après la Première Guerre mondiale, l'inspection de la qualité est devenue plus courante dans les environnements de fabrication et cela a conduit à l'introduction du contrôle statistique de la qualité (SQC), une théorie développée par DR. W. Edwards Deming.
Cette méthode de qualité a fourni une méthode de qualité statistique basée sur l'échantillonnage. Lorsqu'il n'était pas possible d'inspecter chaque élément, un échantillon a été testé pour la qualité. La théorie du SQC était basée sur la notion qu'une variation du processus de production conduit à une variation du produit final.
Si la variation du processus pouvait être supprimée, cela conduirait à un niveau de qualité plus élevé dans le produit final.
Poste de la Seconde Guerre mondiale
Après la Seconde Guerre mondiale, les fabricants industriels au Japon ont produit des articles de mauvaise qualité. Dans une réponse à cela, l'Union japonaise des scientifiques et des ingénieurs a invité Dr. Deming pour former des ingénieurs dans des processus de qualité.
Dans les années 1950, le contrôle de la qualité faisait partie intégrante de la fabrication japonaise et a été adopté par tous les niveaux de travailleurs au sein d'une organisation.
Dans les années 1970, la notion de qualité totale a été discutée. Cela a été considéré comme un contrôle de qualité à l'échelle de l'entreprise qui impliquait tous les employés de la haute direction aux travailleurs, dans le contrôle de la qualité. Au cours de la prochaine décennie, davantage d'entreprises non japonaises introduisaient des procédures de gestion de la qualité en fonction des résultats observés au Japon.
La nouvelle vague de contrôle de la qualité est devenue connue sous le nom de gestion totale de la qualité, qui a été utilisée pour décrire les nombreuses stratégies et techniques axées sur la qualité qui sont devenues le centre de mise au point pour le mouvement de qualité.
Des principes
TQM peut être défini comme la gestion des initiatives et des procédures qui visent à réaliser la livraison de produits et services de qualité. Un certain nombre de principes clés peuvent être identifiés dans la définition de TQM, notamment:
- Gestion exécutive: la direction de haut niveau doit agir comme le principal moteur de TQM et créer un environnement qui garantit son succès.
- Formation: les employés devraient recevoir une formation régulière sur les méthodes et les concepts de qualité.
- Focus client: l'amélioration de la qualité devrait améliorer la satisfaction du client.
- Prise de décision: des décisions de qualité doivent être prises en fonction des mesures.
- Méthodologie et outils: L'utilisation de la méthodologie et des outils appropriés garantit que les incidents non conformes sont identifiés, mesurés et répondus de manière cohérente.
- Amélioration continue: les entreprises devraient continuellement travailler à améliorer les procédures de fabrication et de qualité.
- Culture d'entreprise: la culture de l'entreprise devrait viser à développer la capacité des employés à travailler ensemble pour améliorer la qualité.
- Implication des employés: les employés doivent être encouragés à être proactifs pour identifier et résoudre les problèmes liés à la qualité.
Le coût
De nombreuses entreprises pensent que les coûts de l'introduction de TQM sont bien supérieurs aux avantages qu'elle produira. Cependant, la recherche dans un certain nombre d'industries a des coûts impliqués pour ne rien faire, je.e., Les coûts directs et indirects des problèmes de qualité sont bien plus élevés que les coûts de la mise en œuvre de TQM.
L'expert en qualité américaine, Phil Crosby, a écrit que de nombreuses entreprises ont choisi de payer pour la mauvaise qualité dans ce qu'il a appelé le «prix de la non-conformité."Les coûts sont identifiés dans le modèle de prévention, d'évaluation, d'échec (PAF).
Les coûts de prévention sont associés à la conception, à la mise en œuvre et à la maintenance du système TQM. Ils sont planifiés et engagés avant le fonctionnement réel, et peuvent inclure:
- Exigences du produit: les spécifications de réglage des matériaux, processus et produits finis entrants
- Planification de la qualité: création de plans pour la qualité, la fiabilité, l'opération, la production et les inspections
- Assurance qualité: la création et la maintenance du système de qualité
- Formation: le développement, la préparation et le maintien des processus
Les coûts d'évaluation sont associés aux fournisseurs et aux clients évaluer les matériaux et services achetés pour s'assurer qu'ils sont dans les spécifications. Ils peuvent inclure:
- Vérification: inspection du matériel entrant contre les spécifications convenues
- Audits de qualité: vérifiez que le système de qualité fonctionne correctement
- Évaluation des fournisseurs: évaluation et approbation des fournisseurs
Les coûts de défaillance peuvent être divisés en ceux résultant de la défaillance interne et externe. Les coûts de défaillance internes se produisent lorsque les résultats ne parviennent pas à atteindre les normes de qualité et sont détectés avant d'être expédiés au client. Ceux-ci peuvent inclure:
- Déchets: travail inutile ou détention des actions à la suite d'erreurs ou d'une mauvaise organisation ou d'une communication
- Scrap: produit ou matériau défectueux qui ne peut pas être réparé, utilisé ou vendu
- Reprise: correction du matériel ou des erreurs défectueux
- Analyse des échecs: Ceci est nécessaire pour établir les causes de la défaillance du produit interne
Les coûts de défaillance externes se produisent lorsque les produits ou services n'atteignent pas les normes de qualité mais ne sont détectés qu'après que le client a reçu l'article. Ceux-ci peuvent inclure:
- Réparations: entretien des produits retournés ou sur le site client
- Réclamations de garantie: les articles sont remplacés ou les services repensés sous garantie
- Plaintes: Tous les travaux et coûts associés au traitement des plaintes des clients
- Retours: Transport, enquête et manipulation des articles retournés
Votre chaîne d'approvisionnement optimisée devrait livrer des produits de qualité à temps à vos clients tout en coûtant le moins d'argent possible. TQM vous aidera à atteindre cet objectif.
- « Découvrez les règles de l'agence libre de la Ligue majeure de baseball
- Quelle est la capacité passager des différents modes de transit? »